Molybdenum Disc in Thyristor
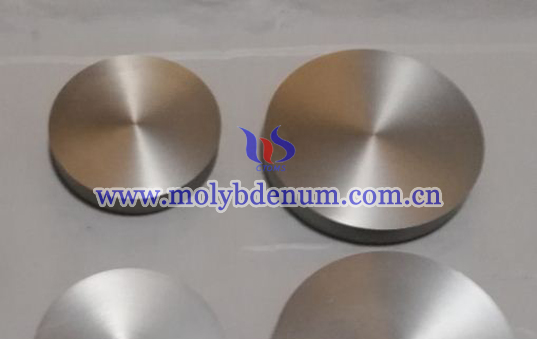
Picture on the right shows a typical construction of a fully floating pressure contact thyristor and the materials used. The silicon wafer is sandwiched between a molybdenum washer and molybdenum disc, thus providing electrical contact to the active parts of the device. These are further sandwiched between two copper pole pieces one in the ceramic housing and the other in the lid. The housing is backfilled with inert gas and the copper lid is cold welded to the ceramic housing. In non-fully floating construction the molybdenum disc is alloyed to the silicon wafer. Electrical and thermal contact is made by clamping the pole pieces under pressure.
Failure of floating pressure contact thyristor is often caused by external accidental event such as particle radiation, voltage transients. Therefore, using molybdenum disc as an insert can decrease such failure effectively.
Material PropertiesLinear coefficient of Material | expansion @ 20°C x106 per °C |
Silicon | 4.2 |
Copper | 16.5 |
Aluminum | 23.95 |
Molybdenum | 5.2 |
Silver | 18.9 |
In a power semiconductor, increases and decreases in the temperature of the device will cause the various internal components to expand and contract. The above table gives the linear temperature coefficient of expansion for materials commonly found inside such devices. In large diameter, high reliability devices, where the internal components are pressed together by a clamp, molybdenum buffers are used between the silicon wafer and the copper electrodes, but in some of the smaller diameter products the copper electrode is in direct contact with the silicon wafer. The difference in the coefficient of thermal expansion causes movement of one component relative to its neighbors with a resultant scrubbing action. This scrubbing will eventually lead to degradation of the device. Molybdenum disc is really a good material for floating pressure contact thyristor